Introduction
Nous avions évoqué, dans notre article sur le dégazeur de radon, la possibilité de récupérer une partie de l’énergie hydraulique procurée par le réseau d’eau courante. Le dégazeur de radon nécessite effectivement de casser la pression de l’eau courante. Cela implique de remettre cette eau en pression, soit par gravité, soit par un surpresseur, lequel implique une dépense d’énergie supplémentaire, notamment d’origine électrique. Nous proposions l’utilisation d’un réservoir gravitaire situé dans les combles pour éviter l’usage d’un surpresseur. La pression perdue, qui n’est pas facturée (puisque l’on paye le volume d’eau mesuré par le compteur), peut être récupérée. Nous proposons la récupération de cette énergie sous forme d’air comprimé, qui peut être stocké progressivement moyennant une rigueur dans l’étanchéité de la réserve et de ses raccords. Cet air comprimé peut servir au bricoleur à faire fonctionner des outils pneumatiques le week-end.
Schéma
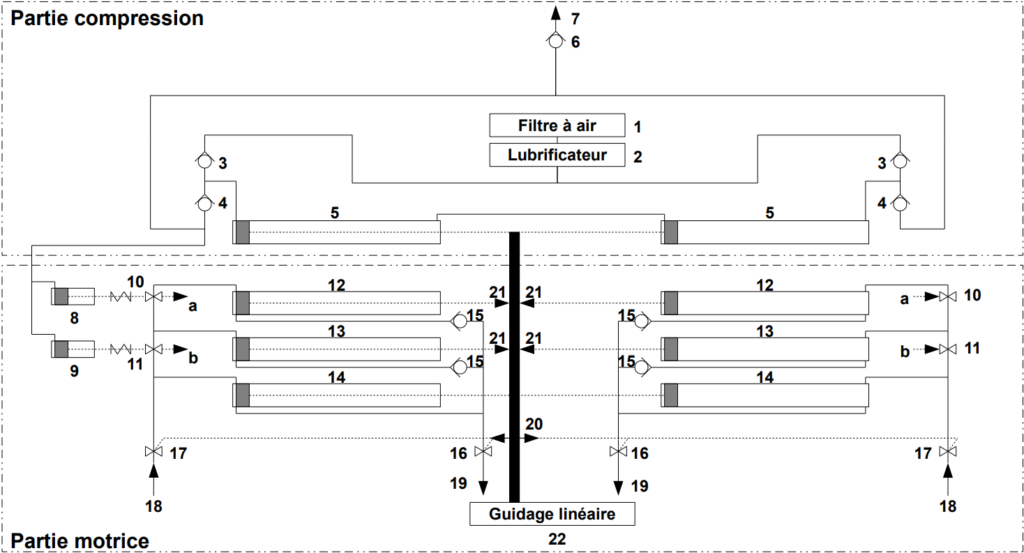
Nomenclature explicative
- Filtre à air : il peut avantageusement être précédé d’un sécheur d’air.
- Lubrificateur d’air : attention, l’usage de lubrificateurs industriels n’est peut être pas adapté car ces derniers fonctionnent en pression, et avec un « fort » débit (effet venturi). Or, nous sommes dans le cas de très petits débits en dépression. Il peut être pertinent de réaliser soi même un lubrificateur adapté.
- Clapets anti retour d’admission.
- Clapets anti retour de refoulement.
- Compresseurs d’air : ils peuvent être réalisés avec des vérins pneumatiques.
- Clapet anti retour avant réserve : il permet d’éviter que les éventuelles légères fuites des raccords des conduits et des compresseurs eux mêmes ne vident la réserve.
- Refoulement vers la réserve : il faut prévoir un décanteur en fond de réserve pour récupérer l’huile. Il peut s’avérer pertinent pour cette dernière, de laisser l’huile y rentrer. Un déshuileur intermédiaire peut être source de fuite, de plus, l’huile peut protéger la réserve de l’oxydation. Dans le cas d’un compresseur lent, un séchage post-compression n’est pas forcément pertinent, puisque les températures de refoulements sont très basses et le débit suffisamment lent pour favoriser le fonctionnement optimal du sécheur pré-compression.
- Détecteur de pression seuil n°1 : il permet de mesurer la pression de refoulement, et ainsi, ouvrir les vannes 10 afin d’activer un vérin moteur supplémentaire. Avec ce principe, nous limitons la dépense d’eau en étant capable de l’adapter, dans une certaine mesure, à la pression de refoulement. Il s’agit d’un petit vérin pneumatique muni d’un ressort calibré de telle sorte qu’il n’ouvre les vannes qu’à partir de la pression de seuil choisie. Pour une compression à 10 bars, nous pouvons utiliser les seuils suivants : de 0 à 4 bars = utilisation d’un seul vérin moteur, de 4 à 7 bars, utilisation de deux vérins moteurs, de 7 à 10 bars, utilisation de trois vérins moteurs. Ces seuils dépendent évidemment de la section des vérins moteurs 12, 13 et 14 ainsi que de la section des vérins compresseurs 5. Ces détecteurs doivent impérativement être connectés avant le clapet anti retour 6, pour que leurs éventuelles légères fuites ne soient que temporaires.
- Détecteur de pression seuil n°2 : il active le dernier vérin moteur disponible.
- Vannes d’alimentation des vérins moteurs 12 : ils correspondent au seuil n°1 et sont activés par les détecteurs de pression de seuil 8.
- Vannes d’alimentation des vérins moteurs 13 : ils correspondent au seuil n°2 et sont activés par les détecteurs de pression de seuil 9.
- Vérins moteurs de seuil n°1 : leur corps (cylindre) peut être réalisé avec un tuyaux en cuivre et leur piston par une rondelle de caoutchouc percée type silentbloc. La tige peut ainsi être réalisée avec une tige filetée en acier inoxydable. En enserrant la rondelle de caoutchouc par des rondelles en acier inoxydable et des écrous freinés, nous pouvons moduler son serrage contre le tuyau. Ceci permet de compenser l’usure et garantir une bonne étanchéité. Il ne serait pas inutile de prévoir un drainage de la légère fuite d’eau possible coté tige. Cette fuite peut être récupérée. Ces vérins moteurs ne sont pas en liaison permanente avec le guidage linéaire, ils utilisent les poussoirs 21, cela évite qu’ils ne soient entrainés lorsqu’ils sont inactifs : la dépression et les frottements bloqueraient le système.
- Vérins moteurs de seuil n°2.
- Vérins moteurs principaux : ils sont en liaison permanente avec le guidage linéaire et donc avec les vérins compresseurs.
- Clapets anti retour : ils empêchent le mouvement parasite des vérins moteurs de seuils n°1 et n°2 lorsqu’ils sont inactifs, au moment de l’échappement des vérins moteurs principaux.
- Vannes d’échappement : elles libèrent l’eau motrice vers le réservoir ou le dégazeur de radon.
- Vannes d’admission : elles alimentent les vérins moteurs avec la pression du réseau d’eau courante.
- Arrivées du réseau d’eau courante.
- Départs de l’échappement : vers la réserve ou le dégazeur de radon.
- Cames : elles actionnent les vannes d’alimentation et d’échappement en fins de courses. L’alimentation et l’échappement en fin de course d’un système à mouvement linéaire composé d’actionneurs à fluide incompressible fera l’objet d’un autre article. Nous avons déjà évoqué cette difficulté dans l’article sur l’élévateur à pistons.
- Poussoirs : ils permettent aux vérins moteurs de seuil n°1 et n°2 de transmettre l’énergie mécanique sans être entrainés par le vérin moteur principal lorsque ce dernier est seul à agir.
- Guidage linéaire : il guide les tiges des vérins moteurs et permet la transmission de puissance mécanique entre les différents éléments.
Conclusion
Ce système peut être utile s’il est surtout réalisé avec des composants peu coûteux, récupérés par exemple. Il est utile si vous souhaitez récupérer la moindre quantité d’énergie à votre disposition. Rappelez vous que l’on paye le volume d’eau, sans considération de la pression à laquelle elle est délivrée chez vous. Si vous utilisez un réducteur de pression dans votre installation, alors cela signifie que vous vous privez d’une certaine quantité d’énergie que l’on peut considérer comme gratuite. Enfin, en comprimant de l’air, vous pouvez utiliser des outils pneumatiques sans utiliser le réseau électrique. L’étanchéité de la réserve d’air comprimé doit être très rigoureuse, pour que ce système ait un véritable sens, parce qu’il fonctionne par une lente accumulation quotidienne de l’air comprimé.