Introduction
Dans la version proposée précédemment, nous avions mentionné plusieurs inconvénients, notamment ceux induits par l’absence de découplage hydraulique. Afin de comprendre pleinement l’intérêt que représente cette nouvelle conception, nous vous invitons à lire l’article précédent.
La volonté d’utiliser des réservoirs de chaleur réalisés avec d’anciens cumulus récupérés nous oblige à obtenir le découplage hydraulique par un système indépendant. En effet, les ballons spécifiques assez coûteux (env. 1 euro par litre) intègrent intrinsèquement la fonction de découplage. Soit par leur effet de « gigantesque bouteille casse pression », soit parce qu’ils comportent directement des échangeurs.
L’usage d’anciens cumulus à une entrée et une sortie implique une certaine gestion de l’équilibrage des pressions/pertes de charge dans le circuit. Cette nécessité interdit en elle même la décorrélation des débits et donc aussi de la puissance consommée relativement à la puissance de la chaudière. En d’autres termes, l’intérêt majeur du stockage qui consiste à possiblement posséder une chaudière « trop puissante » est limité par la notion de limitation du débit maximal dans la chaudière.
Nous proposons de lever cet inconvénient en assumant entièrement la présence d’un découplage hydraulique, via un échangeur externe. Ainsi, la multiplication des ballons de stockage reste financièrement intéressante puisqu’un seul échangeur est nécessaire, indépendamment du volume de stockage, lequel devient extensible à volonté.
Pour la suite de la lecture, veuillez noter que la « réserve de chaleur » ou « réserve » mentionne le composant appelé « ballon tampon » sur le schéma.
Cahier des charges
Avant de critiquer un système quelconque, il convient de connaître avec grande précision le cahier des charges lui correspondant. Dans un système aussi « ramifié » qu’un circuit hydraulique, la moindre différence de cahier des charges peut induire des changements majeurs dans le comportement du système. Nous tenons donc à rappeler ici les contraintes principales du cahier des charges. Si vous découvrez une autre conception plus simple capable de satisfaire ces contraintes et spécifications, merci de nous contacter. Enfin, le fait que la température de départ soit régulée est implicite et n’est pas mentionné dans les contraintes.
Liste des contraintes principales dans le contexte d’utilisation d’une chaudière à bois à hydroaccumulation éventuellement aidée d’un chauffage solaire :
- c.1] Tant que possible, les organes tels que les pompes de circulation et les vannes motorisées seront placés sur les conduites les plus froides (retours) afin d’augmenter leur durée de vie.
- c.2] Le nombre de composants généraux tels que les vases d’expansion, les vannes multi voies et surtout les pompes consommant de l’énergie électrique doit être limité au maximum.
- c.3] L’excédent de chaleur doit être stocké sous la forme d’un volume d’eau le plus faible possible et donc à la température la plus haute possible et admissible par les composants usuels utilisés en technique de chauffage.
- c.4] La puissance de la chaudière à bois pourra être éventuellement très supérieure au besoin théorique calculé pour les locaux, sans générer d’inconfort ni de danger.
- c.5] Lors du démarrage de l’installation, il doit être garanti qu’en tout instant de sa montée en puissance, cette dernière doit être dédiée intégralement au chauffage des locaux. En d’autres termes, aucune puissance ne doit être allouée, à la mise en route, au stockage dans le ballon tampon si le besoin du circuit des émetteurs n’est pas encore couvert.
- c.6] L’accumulateur de chaleur doit pouvoir être constitué de réservoirs simples, à une entrée et une sortie, tels que des ballons d’eau chaude sanitaire électriques récupérés.
- c.7] La réserve de chaleur principale doit pouvoir servir à recharger le ballon d’eau chaude sanitaire et/ou alimenter un récepteur auxiliaire quelconque.
- c.8] L’installation devra comporter une zone d’eau à très basse température (quasi ambiante) permettant l’apport de chaleur solaire ayant pour conséquence une économie de combustible (bois).
- c.9] L’installation devra pouvoir produire de l’eau chaude sanitaire en saison estivale grâce au chauffe-eau solaire, sans générer de fuite de chaleur vers les émetteurs ni vers la chaudière.
Liste des spécifications (méthode imposée, par exemple, si vous souhaitez greffer le système à une partie d’installation déjà existante, sans la modifier) :
s.1] Les émetteurs seront des radiateurs ordinaires munis de robinets thermostatiques deux voies.
s.2] (déjà sous-entendu dans les contraintes) l’eau chaude sanitaire sera produite par un ballon individuel, indépendant de la réserve de chaleur principale.
Schémas
Veuillez noter que ces schémas ne mentionnent pas les accessoires de sécurité et d’agrément tels que les vases d’expansion, soupapes de sécurité, filtres, vannes d’isolement, etc. Cette version allégée permet de faciliter la compréhension de la logique de fonctionnement.
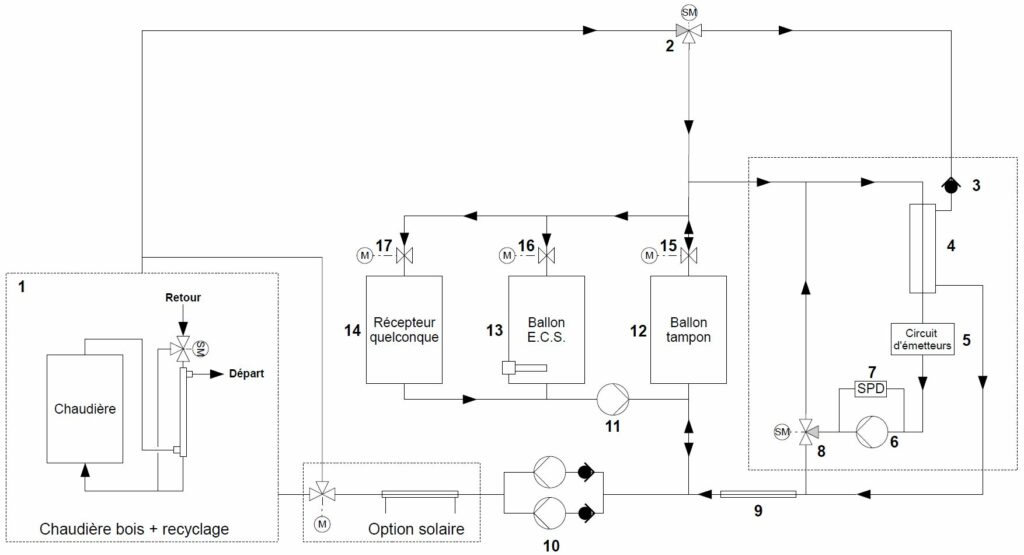
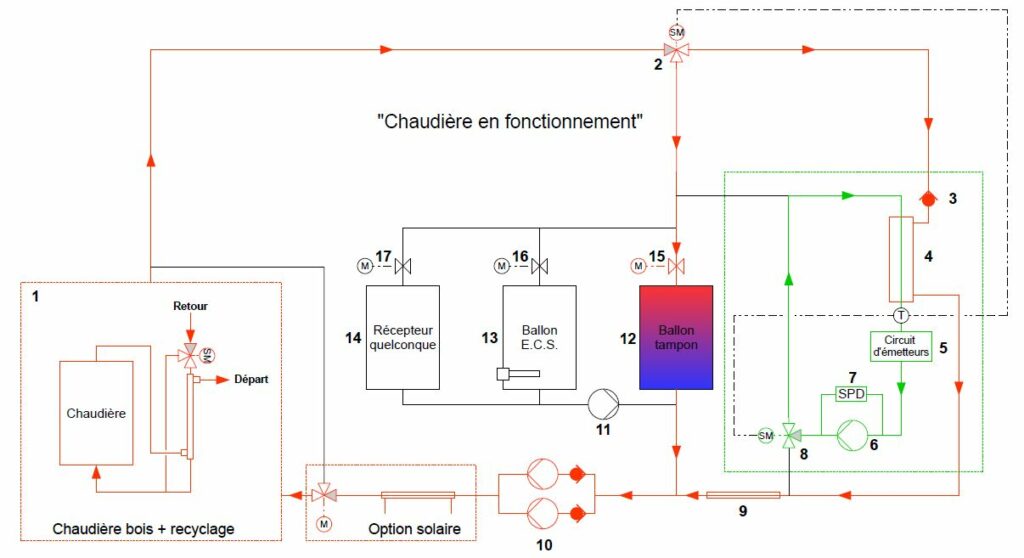
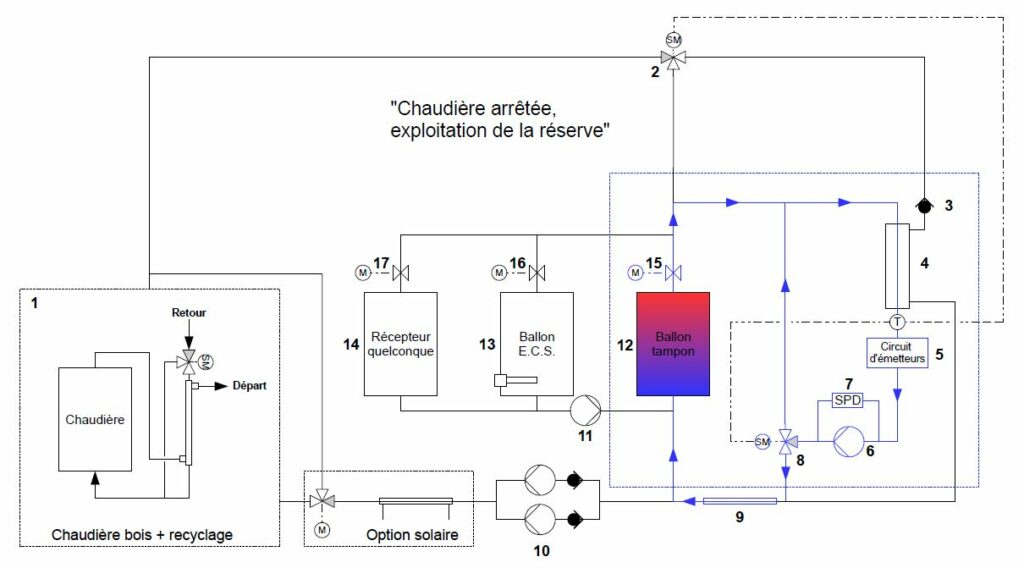
Réponses aux contraintes et spécifications
- Contrairement à la proposition précédente il n’est plus nécessaire d’avoir recours à des robinets thermostatiques à trois voies. Les débits étant décorrélés, ils peuvent donc être différents entre le circuit des émetteurs et le reste du système. Il devient donc possible d’avoir une différence de puissance importante entre le besoin de l’habitation et la chaudière, tout en optimisant le rendement de cette dernière. Nous respectons ainsi la contrainte c.4.
- Le circuit des émetteurs étant constitué de radiateurs à vannes thermostatiques à deux voies conventionnelles, il peut se fermer totalement. De ce fait, l’ajout d’une soupape de pression différentielle est nécessaire. Nous pouvons respecter ainsi la spécification s.1. En faisant varier le débit grâce à ces robinets thermostatiques, nous évitons le paradoxe qui consiste à envoyer au retour, de l’eau encore chaude n’étant passée dans aucun radiateur. Ceci est un critère favorisant la respect de la contrainte c.8.
- Seuls les débits sont découplés, le circuit reste à une seule pression statique globale commune. Cela permet d’éviter de multiplier les accessoires comme les soupapes de sécurité, les filtres et les vases d’expansion et donc de réduire les coûts. Nous répondons ainsi à la contrainte c.2. Ceci ne serait pas forcément le cas avec des installations conventionnelles, utilisant des ballons tampon avec échangeurs intégrés.
- La régulation de température au départ des émetteurs se fait, lorsque la chaudière est en fonctionnement, par variation du débit qui est alloué à l’échangeur thermique (repère 4). Avec ce fonctionnement, il est obligatoire de conserver une température de départ vers les émetteurs inférieure à la température maximale du primaire. En effet, si le débit primaire (chaudière) de l’échangeur devient supérieur à celui du secondaire (circuit d’émetteurs), plus aucune variation de température ne sera possible au secondaire. La régulation enverra donc tout le débit de la chaudière dans l’échangeur. Dans un tel cas, la température de l’eau du circuit primaire, sortant de l’échangeur 4, ne serait plus du tout maîtrisée et serait alors trop élevée.
- Nous pouvons considérer, comme inconvénient, l’utilisation de deux vannes distinctes dédiées à la même fonction : la régulation de la température de départ. En effet, les deux modes de fonctionnement induisent cette nécessité : le mode chaudière en fonctionnement et le mode exploitation de la réserve. Ceci est une conséquence directe de l’utilisation de l’échangeur thermique. En mode chauffage avec la chaudière en fonctionnement, la vanne trois voies 2 répartit l’eau chaude entre le ballon tampon et l’échangeur, en mesurant la température de départ vers les émetteurs. Cette valeur de consigne peut être variable, notamment si elle est pilotée par un régulateur type RVL ou définie manuellement par l’utilisateur. Dans la phase « chaudière en fonctionnement » la vanne trois voies 8 est en butée, elle boucle perpétuellement le circuit des émetteurs. C’est donc la température mesurée au départ du circuit des émetteurs et le ressenti des habitants du bâtiment qui la choisissent, qui quantifie l’excédent de chaleur envoyé dans le ballon tampon.
- Sur ce schéma, nous avons intentionnellement représenté deux circulateurs (repère 10) dans la boucle de la chaudière, afin de spécifier que le débit du circuit primaire (chaudière) peut être tout à fait différent de celui du circuit des émetteurs. Ce découplage est l’objectif recherché. Ainsi la chaudière peut être dimensionnée n’importe comment tant que sa puissance nominale est supérieure à celle demandée par le circuit des émetteurs. Il est évident qu’il faudra adapter le volume du ballon tampon à la chaudière.
- Les vannes motorisées 15, 16 et 17 sont installées sur la conduite chaude malgré la contrainte c.1 afin d’empêcher d’éventuels effets de thermosiphon. La vanne trois voies 2 ne peut pas non plus être placée en « décharge inversée » , au retour. Elle empêcherait effectivement le passage de l’eau de retour vers le ballon lors du fonctionnement « chaudière à l’arrêt ».
Pourquoi les schémas comme celui-ci ne nous conviennent pas ?
Pourtant répandus sur le net, dans les forums et même sur les sites de professionnels, ces schémas sont souvent partiellement défaillants. Ils impliquent des spécificités nécessaires à leur fonctionnement, lesquelles ne sont presque jamais évoquées clairement. Les installations réalisées de cette manière fonctionnent souvent de façon non optimale, »sur un malentendu ».
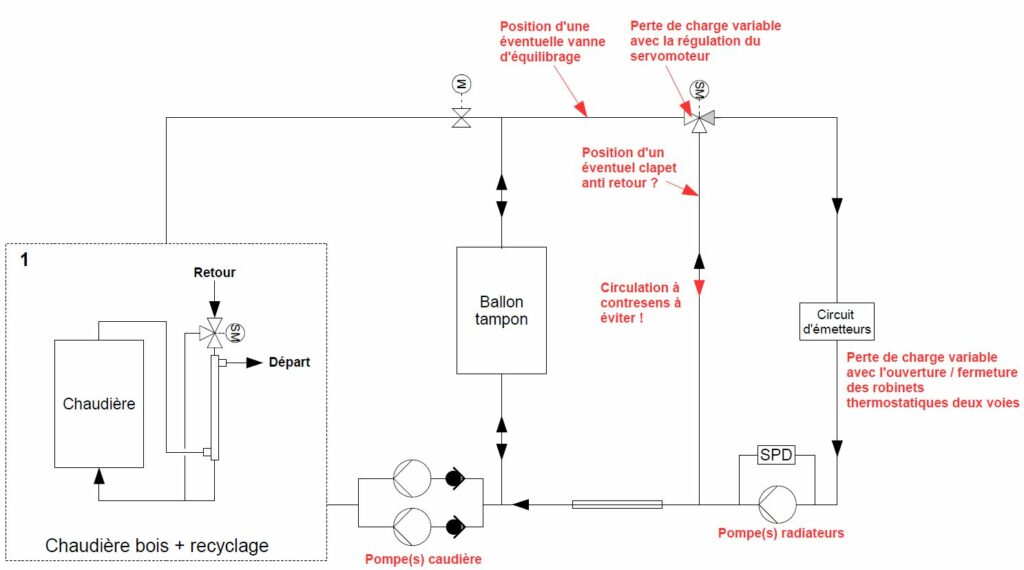
Ce genre de schéma devrait toujours être accompagné des remarques suivantes :
- L’ajout d’une vanne d’équilibrage assurerait une singularité fixe, laquelle, au démarrage de l’installation, pourrait limiter le débit dans le circuit des émetteurs, et donc la puissance thermique dans l’habitation.
- La plage dans laquelle la vanne trois voies est capable de réguler peut être potentiellement réduite.
- Une circulation à contresens dans la branche de recyclage (voir schéma), induirait une température maximale au départ du circuit des émetteurs sur une certaine plage de régulation. Cette circulation cesserait dès lors que la perte de charge intrinsèque de la vanne trois voies serait suffisamment élevée.
- La circulation à contresens injecterait alors de l’eau chaude dans le retour, défavorisant l’utilisation d’un échangeur solaire en réchauffage de retour, par exemple. De plus, quelles seraient les conséquences sur l’exploitation optimale de la chaudière ? Cela n’optimiserait pas le stockage de la chaleur, évidemment.
- Avec un clapet anti-retour, on interdirait cette circulation inverse, mais le problème de la régulation partielle persisterait.
- La variation de perte de charge dans le circuit des émetteurs à robinets thermostatiques à deux voies réduirait, elle aussi, la contre-influence de la pompe sur les débits et pressions imposés par l’autre pompe, celle de la chaudière.
Pourquoi ce type d’installation semble fonctionner dans la plupart des cas ?
- Parce que souvent, les pompes de la chaudière et du circuit des émetteurs sont de puissances comparables, voire identiques. Mais cette puissance comparable induit une potentielle non exploitation de la puissance nominale de la chaudière et interdit un éventuel surdimensionnement (chaudière récupérée, bonne affaire, etc.).
- Parce que les réglages manuels que l’on peut faire sur les vannes d’équilibrage éventuelles égalisent grossièrement les pertes de charge. Cependant, cela induit encore une fois une non optimisation de l’utilisation de l’installation. Par exemple au démarrage, en restreignant le débit vers les émetteurs.
- Parce qu’il est parfois difficile de visualiser un dysfonctionnement. Si la régulation est inopérante par moment, le particulier non averti ne s’apercevra pas que ce sont les robinets thermostatiques qui agissent et que la vanne trois voies est devenue inutile.
- etc.
Tout cela est donc du « bidouillage » ! Si vous êtes prêt à acheter un ballon de stockage spécifique, le mieux est d’en choisir un capable de réaliser un découplage hydraulique, avec plusieurs entrées et sorties. Si vous tenez, comme suggéré, à utiliser des réservoirs récupérés ne possédant qu’une entrée et une sortie, nous vous recommandons notre schéma. Ce dernier garantit une maîtrise entière des contraintes mentionnées dans notre cahier des charges en haut de page.
Avertissement sur la théorie des vannes trois voies et les circulations parasites
Les vannes mélangeuses à trois voies, utilisées en chauffage sont précisément prévues pour mélanger les débits. En conséquence, très souvent, elles ne sont pas étanches en fin de course (butée à gauche ou butée à droite) car cela est considéré comme non indispensable au regard de leur fonction principale. Cela signifie qu’il peut rester de légères circulations parasites dans certaines branches du circuit à des moments où l’on ne le souhaite pas. Ces fuites ne sont pas acceptables dans le cadre du système que nous vous proposons, car la fermeture totale d’une voie est un élément de logique à part entière utilisé dans la conception du système.
D’une façon générale, nous vous recommandons d’utiliser des vannes de bonne qualité. Pour savoir si une vanne trois voies est suffisamment étanche, nous n’avons pas le choix, il faut l’examiner dans le détail. Les vannes qui possèdent un ressort sont en général suffisamment étanches. Ce ressort maintient le secteur plaqué contre son siège, induisant une étanchéité suffisante dans le cadre d’un aiguillage de débit. Ce n’est pas le cas de toutes les vannes trois voies.
Dans notre cas, la circulation parasite la plus délétère est celle qui provoquerait un réchauffement accidentel du circuit des émetteurs en saison estivale, où l’on utiliserait l’installation uniquement pour la production d’eau chaude sanitaire. Nous devrions donc isoler par une autre vanne motorisée la boucle du circuit des émetteurs, côté chaud, ceci afin d’éviter les effets de thermosiphon. Le clapet anti retour 3, quant à lui, a pour rôle d’éviter un effet de thermosiphon interne à la conduite située en amont de l’échangeur 4, y compris en saison de chauffe, lors de l’exploitation de la réserve. Selon la disposition mécanique réelle de l’installation, il peut être monté sur la conduite en provenance de la chaudière, juste avant la vanne trois voies 2, car la conduite située au dessus du ballon tampon peut aussi générer des déperditions.
Nous proposons alors cette alternative qui permet d’entraver les thermosiphons parasites en saison estivale, en ayant déplacé la vanne trois voies 8 sur la conduite chaude :
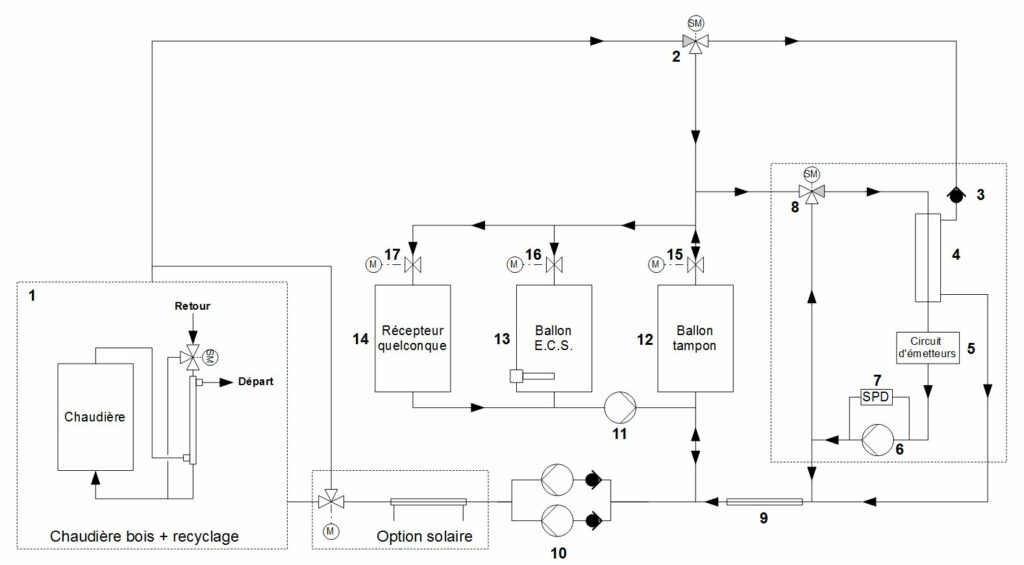
Qu’en est-il si nous souhaitions utiliser une bouteille de découplage hydraulique ?
Il semble qu’il soit aussi possible d’utiliser une bouteille de découplage hydraulique, également appelée « bouteille de mélange » ou « bouteille casse pression différentielle » à la place de l’échangeur.
Cependant, le « pouvoir de découplage » d’un échangeur reste supérieur à celui d’une bouteille de mélange. En effet, avec un échangeur, la pression statique locale est possiblement différente entre le primaire et le secondaire, alors qu’avec une bouteille, elle est obligatoirement commune. Il se dit souvent d’une bouteille de mélange qu’elle a pour but de créer un « point neutre » entre deux circuits. En conséquence, il faut ajouter un train de vannes motorisées supplémentaire pour gérer ce découplage moindre. Ce train de vannes doit s’actionner au moment des passages entre les deux modes de fonctionnement chaudière/réserve.
Moyennant une complexité plus élevée, nous obtenons plusieurs avantages, qui ne sont autres que ceux habituellement attribués aux bouteilles de mélange. Parmi eux, se trouvent principalement : une insensibilité aux saletés, puisque la bouteille permet même de les faire décanter, la faculté à dégazer facilement le réseau en plaçant un purgeur au sommet, une robustesse intrinsèque largement supérieure à celle d’un échangeur à plaques notamment. De plus, une bouteille de mélange peut tout à fait se fabriquer facilement compte tenu de sa simplicité conceptuelle.
Attention cependant à bien comprendre la différence de fonctionnent avec un échangeur. Avec une bouteille de découplage, c’est le mélange d’eau, interdit avec un échangeur, qui mélange aussi la chaleur. Nous pouvons aussi noter que le rendement est de 100% puisque le mélange de la chaleur se fait directement par le mélange du fluide.
Attention, pour que la bouteille de mélange réponde au fonctionnement demandé par notre cahier des charges, le débit du secondaire doit toujours être supérieur au débit qui provient du primaire, et qui est délivré par la vanne trois voies motorisée (celle du primaire). En effet, si ce débit primaire était supérieur à celui du secondaire, il n’y aurait plus de mélange au départ du secondaire. La température serait alors la température maxi chaudière. De plus, le retour au primaire contiendrait une fraction d’eau chaude. Ce que nous nous sommes interdit dans notre cahier des charges. Heureusement, tant que la consigne de la température de départ est inférieure à celle du primaire, il y a obligatoirement mélange au départ du secondaire. Le flux vertical, dans une bouteille de découplage hydraulique, ne peut en aucun cas être simultanément montant et descendant. Tant qu’il sera montant, il n’y aura pas de recyclage d’eau chaude au primaire.
Pour bien comprendre le sens des propos ci-dessus, nous vous conseillons vivement de regarder cette vidéo.
Attention ! Il est important de placer la sonde de température de départ assez loin de la bouteille, après une singularité comme un coude par exemple. En effet, souvent, les chauffagistes comptent sur la pompe de circulation pour mélanger correctement l’eau chaude et froide. Sauf que, dans notre cas, la pompe est située au retour (pour qu’elle soit soumise à de faibles températures). Il peut convenir d’installer une singularité intentionnelle, tel un petit morceau de tôle hélicoïdal dans le tuyau de départ afin de créer un mélange correct avant la sonde de température.
Nous obtenons le schéma suivant :
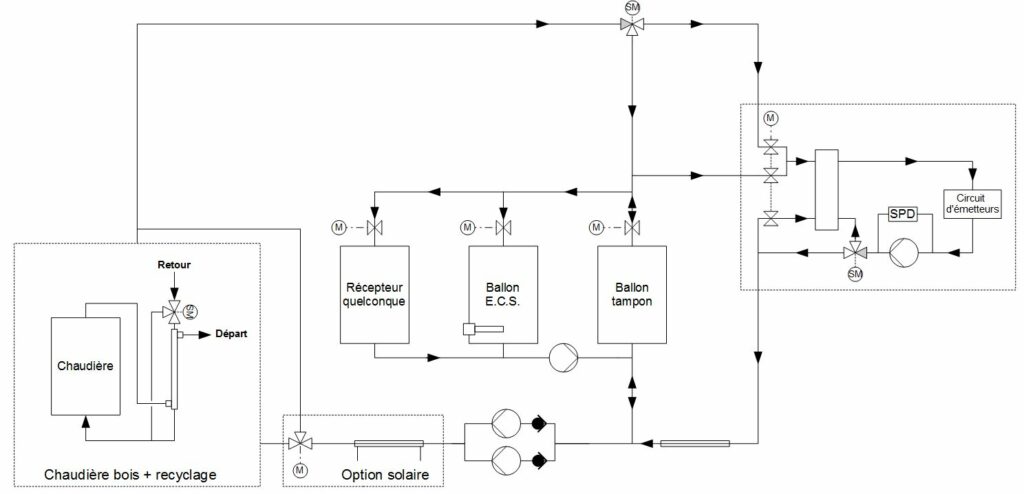
Conclusion
Il est relativement facile de répondre à un cahier des charges complexe par la complexité elle-même. Il est facile de satisfaire notre cahier des charges en ajoutant une grande quantité de vannes motorisées. Ce qui est en revanche moins évident c’est de trouver la combinaison idéale de composants juste nécessaire au respect d’un cahier des charges donné. N’hésitez pas à nous contacter si vous décelez une incohérence dans notre schéma, ou si vous pensez qu’il reste des simplifications possibles.