Introduction
Le gazogène, nous l’avons déjà évoqué dans l’article sur le mimétisme technologique. Contrairement à son usage le plus répandu dans le domaine des loisirs techniques, nous proposons une version destinée au chauffage des habitations. Notez que les installations stationnaires de gazogènes sont particulièrement répandues en Allemagne et en Autriche. On les appelle en général « centrales de cogénération à biomasse ». En effet, dans ces installations, la biomasse (bois déchiqueté) est gazéifié puis injecté dans des groupes électro-générateurs dont les pertes en chaleur sont valorisées.
En revanche, notre cas ci-proposé devrait être qualifié de « chaudière à gaz de bois, à condensation ». Cette technologie cumule les avantages d’une chaudière à plaquette de bois (souvent très coûteuse) à ceux d’une chaudière à condensation pour ce qui est du rendement énergétique. De plus, la plaquette forestière est actuellement (2020) l’énergie bois la moins cher au kWh.
Avertissements
Le schéma et les explications ci-dessous ne sont jamais qu’une suggestion de conception. Elle n’intègre en aucun cas la description des organes et mesures de sécurité totalement indispensables dans une tel projet.
Il y a en effet des dangers mortels tels que l’asphyxie, l’intoxication au monoxyde de carbone, les explosions, brûlures, etc.
Une telle installation n’est donc absolument pas utilisable en l’état, telle que présentée dans cet article.
Il ne s’agit encore une fois que d’une description sommaire de ce que serait une hypothétique installation de chauffage à gaz de bois. Un tel dispositif ne devrait en aucun cas se situer dans un local d’habitation.
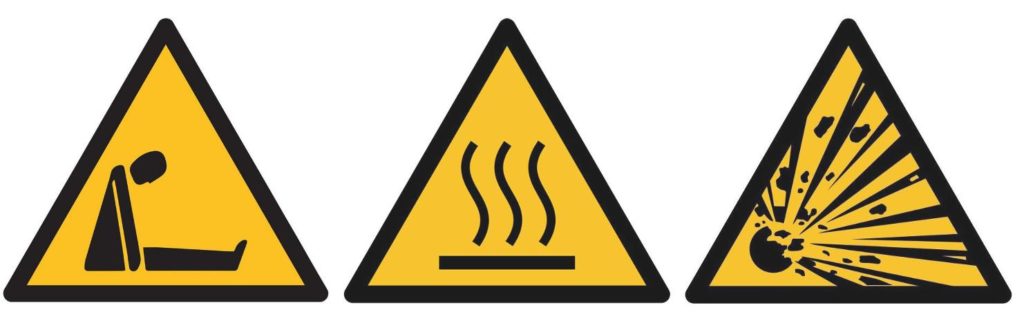
Schéma

Nomenclatures explicatives
1. Gazéification
- 1.1 Structure principale externe du silo à plaquettes : réalisée avec un ensemble mécanosoudé de cornières en acier, elle peut ensuite être comblée de briques en béton cellulaire. Le béton cellulaire est un excellent isolant thermique résistant à la chaleur. Le tout peut ensuite être peint voire enduit.
- 1.2 Couvercle isolé supérieur : recouvert de laine de verre (ou de roche), il permet d’isoler le couvercle du silo. Cela permet de minimiser la condensation. Il ne faut pas oublier que le couvercle sera manipulé à chaque recharge du silo.
- 1.3 Couvercle du silo : il s’agit du couvercle du fut qui garantit l’étanchéité du silo.
- 1.4 Soupape de sécurité : accessoire de sécurité indispensable, il limite la pression dans le silo en cas de déflagration. Cette dernière pourrait survenir en fonctionnement par une intrusion d’air impromptue. Pour cette raison il est recommandé d’inter-verrouiller le couvercle 1.2. C’est à dire d’empêcher son ouverture en cours de fonctionnement comme cela se pratique sur les lave-linges, via des mécanismes spécifiques.
- 1.5 Poids presseur : il facilite la descente des plaquettes en réduisant la formation d’un cône vide au centre du silo.
- 1.6 Espace utile du silo : c’est la zone de réserve des plaquettes de bois dont le niveau baisse au fur et à mesure de la gazéification.
- 1.7 Isolant thermique : cet isolant est celui de partie haute du silo, soumis à des températures moindres qu’au niveau du foyer. Il peut éventuellement être de nature différente que l’isolant 1.13.
- 1.8 Allumeur : il permet l’inflammation des plaquettes de bois et n’entre en action que dans le cadre d’un cycle d’allumage. Il pourrait être constitué d’un système d’injection d’air chaud, ce qui est le cas dans certaines chaudières à pellets. Cependant, compte tenu de la distance importante que l’air doit parcourir dans la masse de béton réfractaire, il pourrait avoir suffisamment chuté en température pour ne plus permettre l’incandescence du bois. Un tel dispositif devrait être monté provisoirement en série avec l’air principal via un bypasse lors de la procédure d’allumage. Une autre méthode est l’injection d’un combustible liquide ou l’introduction d’une flamme de gaz. C’est plutôt à ces deux dernières options que correspond le schéma.
- 1.9 Arrivée d’air : il s’agit de la conduite principale d’alimentation en air du foyer du gazogène.
- 1.10 Foyer : c’est la zone où les plaquettes de bois sont pyrolysées.
- 1.11 Corps du foyer : en béton réfractaire, réalisé avec du fondu, de la chamotte, et de la vermiculite (ou de la pouzzolane), il est coulé sur des contre-formes (en polystyrène par exemple, ensuite dissoutes à l’aide d’acétone) et en emprisonnant les conduites d’arrivée d’air. La forme en diabolo est indispensable pour éviter la formation excessive de goudrons. En effet, elle contraint l’intégralité des gaz à passer par le centre chaud du foyer, favorisant ainsi le craquage.
- 1.12 Distributeur torique : il répartit toutes les buses d’injection d’air autour du foyer, garantissant son homogénéité et permettant ainsi la descente facile des plaquettes de bois.
- 1.13 Isolant thermique : devant résister aussi à des hautes températures, il est recommandé qu’il soit constitué du même béton réfractaire que la structure du foyer 1.11.
- 1.14 Agitateur : il permet de secouer périodiquement le plateau 1.15 afin d’éviter le colmatage .
- 1.15 Plateau : il retient les charbons produits par le foyer, afin de les maintenir à haute température et dans la trajectoire des gaz, car ils y jouent le rôle primordial de réducteur.
- 1.16 Grille de filtration : elle constitue le premier système de filtration du gaz, empêchant l’aspiration de charbons grossiers.
- 1.17 Structure de l’embase : elle peut être constituée d’une dalle en béton coffrée, ou d’une plaque métallique par exemple.
- 1.18 Couvercle isolé inférieur : muni d’un isolant thermique, il a la même fonction que le couvercle supérieur 1.2.
- 1.19 Couvercle du cendrier : il garantit l’étanchéité du cendrier tout en facilitant le décendrage et la maintenance.
- 1.20 Espace cendrier : il permet de recueillir les cendres tombées du plateau, c’est aussi depuis cet endroit qu’est aspiré le gaz produit.
- 1.21 Structure portante : en poutrages bois, IPN, mécanosoudure, pieds de bureaux, etc.
- 1.22 Conduite de transfert : elle doit impérativement être isolée thermiquement et posséder une cassure avec des raccords en té, ou un raccord en croix. Elle doit pouvoir être inspectée et nettoyée par le biais de bouchons de visite. Ces bouchons doivent être étanches mais résistants aux très hautes températures (env.600°C). De ce fait, l’étanchéité devra être effectuée par des joints métalliques, en bronze par exemple, sur des surfaces rigoureusement planes.
2. Filtration
- Avants propos : la structure globale du filtre n’est pas abordée, elle est sensiblement la même que celle de la partie gazéification. Il est même possible de couler le béton réfractaire de telle sorte à ce que la partie filtration et gazéification soient comprises dans la même structure.
- 2.1 Récupérateur de poussières : il permet de récupérer les cendres fines centrifugées dans le cyclone 2.2 ainsi que les éventuels condensats. Les condensats doivent être minimes à cet endroit car l’isolation thermique doit maintenir les gaz à la température la plus élevée jusqu’à leur sortie de la filtration.
- 2.2 Cyclone : il permet de centrifuger les particules les plus lourdes qui tombent ensuite dans le récupérateur 2.1.
- 2.3 Grille : elle retient les éléments filtrants en laissant passer le gaz.
- 2.4 Charbon : premier élément filtrant, le charbon de bois bon marché se remplace à moindres frais.
- 2.5 Second média : le second et le troisième média de filtration peuvent être constitués de matières minérales comme la pouzzolane, la zéolithe ou l’argile sous forme de billes. Bon marchés et résistants aux très hautes températures, ils assurent la propreté des échangeurs de la partie refroidissement.
- 2.6 Troisième média : le troisième média de filtration est optionnel, de manière logique il doit toujours être plus fin que le précédent, ce peut être de la zéolithe si le média précédent était constitué de pouzzolane, par exemple.
- 2.7 Couvercle du filtre : très étanche, il doit aussi résister à des températures de l’ordre de plusieurs centaines de degrés Celsius. Un joint métallique est dans ce cas aussi de mise.
- 2.8 Couvercle isolé : recouvert de laine de verre (ou de roche), il permet d’isoler le couvercle du filtre 2.7.
- 2.9 Conduite de descente : elle permet de déplacer la sortie des gaz vers le bas, principalement pour les besoins de disposition de la partie refroidissement.
3. Refroidissement
- 3.1 Échangeur air/gaz : l’objectif principal de cet échangeur est de maximiser la température d’entrée de l’air dans le gazogène, réduisant à priori la formation de goudrons. La température du gaz produit s’en trouve néanmoins abaissée.
- 3.2 Échangeur eau/gaz : l’objectif de cet échangeur est de refroidir efficacement le gaz. L’eau qui circule dans cet échangeur est prélevée sur le retour du circuit hydraulique du chauffage central. En règle générale, le gaz ne pourra jamais descendre en dessous de 50°C à la sortie de cet échangeur, c’est une température usuelle de retour d’un circuit de chauffage standard.
- 3.3 Échangeur air/gaz : comme l’air ambiant est normalement inférieur à la température du gaz en sortie de l’échangeur 3.2, on refroidit encore le gaz. Cependant, dans un hypothétique cas idéal d’un échange efficace à 100% (et de caractéristiques identiques de l’air et du gaz de bois), la température du gaz restera toujours supérieure à celle de l’air, puisque le débit de gaz est forcément plus élevé que le débit d’air.
- 3.4 Échangeur air/gaz : cet échangeur final n’évacue pas de calories du système global, il permet surtout le réglage de la différence de température entre l’air envoyé au brûleur et le gaz. Ceci est important car le mélange air/gaz dans le brûleur se fait de manière optimale à une valeur de différence précise de température. Il conviendra de la trouver au moment du réglage du brûleur.
- 3.5 Vanne motorisée : cette vanne motorisée ne s’utilise pas en régulation mais en tout ou rien, elle ferme l’arrivée d’air pour arrêter le gazogène et l’ouvre au moment de la procédure de démarrage.
- 3.6 Filtre à air : il protège la canalisation d’arrivée d’air de l’encrassement.
- 3.7 Filtre à air : il protège les canalisations et le brûleur de l’intrusion de poussières. Il convient de l’adapter au débit d’air élevé demandé par le brûleur.
- 3.8 Récupérateur de condensat : il récupère les condensats générés dans l’échangeur 3.1 mais aussi ceux éventuellement générés par la conduite de descente 2.9, il doit être impérativement étanche.
- 3.9 Récupérateur de condensat : il récupère les condensats générés dans les échangeurs 3.2 et 3.3, il doit être impérativement étanche. Les récupérateurs de condensats 3.8 et 3.9 ne peuvent en aucun cas être communs.
4. Conditionnement et exploitation
- 4.1 Mitigeur d’air : il permet de régler la différence de température entre le gaz et l’air, ce qui permet d’optimiser le fonctionnement du brûleur.
- 4.2 Filtre final : constitué d’un vide cendre dont l’étanchéité parfaite a impérativement été vérifiée, c’est le dernier filtre avant le brûleur. Ce vide cendre à usage détourné récupère aussi les éventuels condensats résiduels.
- 4.3 Turbine air : elle fournit le brûleur en air de combustion et l’excès est utilisé en tirage induit dans le conduit de fumées 4.15. Il convient donc de s’assurer que son débit est suffisant à satisfaire les deux besoins. Si la turbine est surdimensionnée, il se peut que le tirage induit génère un débit supplémentaire non désiré au niveau du brûleur. Une vanne de restriction générale peut alors être ajoutée. Le rendement du tirage induit est forcément moindre que l’injection direct d’air dans le brûleur. C’est ce qui permet d’effectuer un réglage avec une telle disposition.
- 4.4 Turbine gaz : c’est la turbine qui aspire le gaz au travers de l’ensemble du système. Cette dernière doit être absolument étanche et donc de construction qualitative. Une turbine du même type que celles utilisées dans les cabinets dentaires peut convenir.
- 4.5 Clapet anti retour : par mesure de sécurité, en cas de déflagration, de retour de gaz, ou de panne de moteur de la turbine 4.3, il protège cette dernière ainsi que le circuit d’air.
- 4.6 Clapet anti retour : il assure la même fonction que le clapet anti retour 4.5 du circuit d’air et évite surtout un retour de gaz de la réserve 4.9.
- 4.7 Vanne motorisée : elle permet d’orienter le gaz vers le brûleur ou vers le torchère de démarrage 4.9. Elle s’utilise en tout ou rien.
- 4.8 Clapet anti retour : il évite un retour de flamme du torchère 4.8, il doit être complété par une grille anti retour.
- 4.9 Torchère de démarrage : il reçoit les gaz produits pendant la phase de démarrage et intègre une veilleuse qui tente continuellement d’allumer les gaz. Un système de détection de flamme (thermocouple ou optique) signale ensuite à la partie commande la présence de la flamme. Le cycle de démarrage du brûleur pourra alors commencer.
- 4.10 Réservoir de pression : il permet de stocker une légère quantité de gaz en amont du brûleur, ce qui permet d’alimenter pendant de courts instants le régulateur de pression 4.11.
- 4.11 Régulateur de pression : il permet, avec l’aide de la réserve 4.10, d’effacer temporairement une baisse de débit de gaz. En effet, l’évolution du foyer dans le gazogène conserve toujours un côté aléatoire propre au procédé. Il peut par exemple être constitué d’un soufflet de suspension de camion, qui capte la pression de sortie vers le brûleur puis agit sur une vanne sphérique.
- 4.12 Répartiteur : il permet de répartir le flux d’air entre le brûleur (fraction destinée à la combustion) et l’extracteur de tirage induit 4.16.
- 4.13 Brûleur : le brûleur mélange l’air et le gaz dans des conditions optimales, c’est un sujet à part entière. Un brûleur à gaz de bois doit être structuré très différemment d’un brûleur à gaz naturel ou à propane, le gaz de bois étant de nature très différente et contenant notamment du diazote.
- 4.14 Chaudière : c’est une chaudière pouvant recevoir un brûleur à air soufflé. Il peut donc aussi bien s’agir d’une chaudière à gaz que d’une une chaudière à fioul.
- 4.15 Échangeur : c’est l’échangeur qui permet de transformer la chaudière en version condensation.
- 4.16 Conduit d’extraction : il permet d’extraire les fumées refroidies, comme dans toutes chaudière à condensation, par l’intermédiaire d’une extraction forcée. Dans ce cas, il s’agit d’une extraction par tirage induit via la turbine 4.3.
Conclusion
Nous pourrions prendre peur en voyant la complexité apparente du schéma d’une telle installation. Mais en réalité, c’est une fois de plus la recontextualisation de certains composants qui permettrait de la réaliser relativement simplement. Comme nous l’avons mentionné avant, une telle installation comporte des risques. Il serait nécessaire de traiter aussi de la manière avec laquelle la recontextualisation d’autres composants gèrerait l’aspect sécurité. En effet, il existe des microcontrôleurs et capteurs accessibles aux particuliers. Il devient rapidement possible de se mettre en sécurité par la redondance des systèmes de détection des fuites de gaz par exemple. Comme on le pratique dans l’industrie, plusieurs contrôleurs devraient effectuer les mêmes tâches de mesure simultanément. C’est la redondance qui permettrait, dans un contexte de loisirs techniques, de gérer correctement l’aspect sécurité (lié à la détection). Il conviendrait de continuer à utiliser cette philosophie aussi dans l’aspect commande du système. Dans ce cas, les bonnes pratiques de programmation rigoureuses, n’étant que conceptuelles, ne rencontrent aucunes barrières à leur application dans le cadre d’une réalisation non industrielle. Nous n’avons pas présenté de suggestion de conception d’un brûleur adapté au gaz de bois, ce que nous ferons peut être dans la cadre d’un autre article.